Astúries era carbó i acer i ara, dels dos, només queda ja l'acer, però no un acer qualsevol: a més de l'única siderúrgia integral de tota la península (la planta de Veriña), el Principat acull en Avilès modernes acereries i un centre d'innovació tecnològica en el qual es desenvolupen productes de tota mena i es testen tecnologies disruptives com la impressió 3D. Aquesta última tècnica, precisament, és la que s'ha utilitzat per fabricar components que ha utilitzat un dels vehicles que han competit en l'última edició del Dakar.
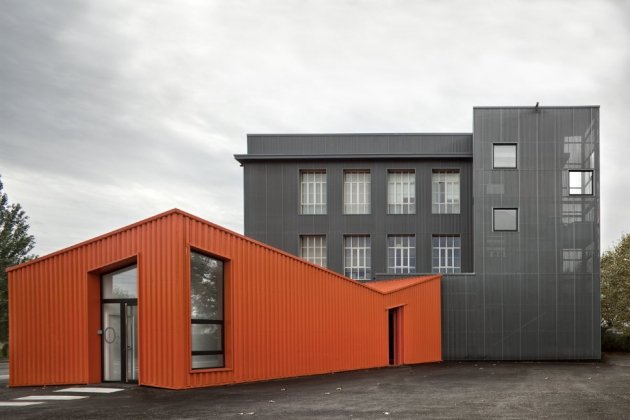
Els ancoratges d'un direccionador
Les peces construïdes a Arcelor Mittal Avilés formen part del sistema d'ancoratge dels direccionadors laterals del Sodicars número 56 amb què els habitants de Conca Manolo i Mónica Plaza (la seva filla) han competit aquest any en el ral·li. Plaça, propietari d'una agència de viatges d'aventura, acumula amb la d'aquest any catorze participacions en el Dakar. La peça d'acer fabricada en Avilès amb impressió 3D ha superat el test: els seus 800 grams (un 20% menys del que pesaria un component fabricat en alumini amb mètodes tradicionals) no ha plantejat cap problema.
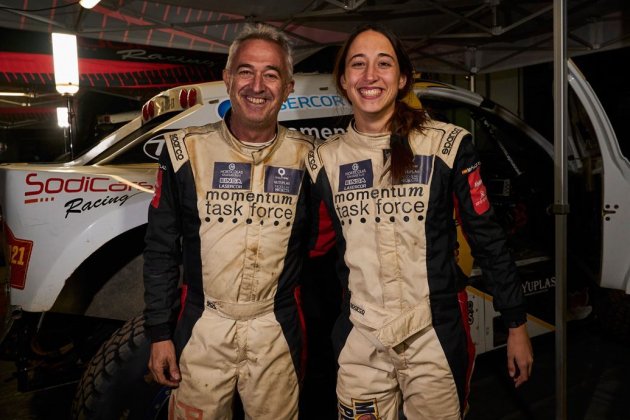
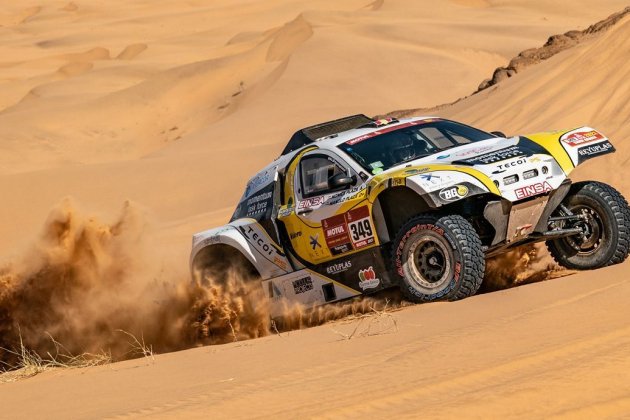
Nous camins
L'èxit, obre sens dubte un nou nínxol de negoci per a Arcelor Mittal, que pot sense problemes oferir solucions dissenyades digitalment i construïdes mitjançant fabricació additiva a tots els sectors que s'atreveixin amb aquest nou sistema. "En la mobilitat futura, la fabricació additiva continuarà tenint un gran paper i l'acer continuarà reinventant-se per aprofitar noves oportunitats de desenvolupament", expliquen des d'Arcelor Mittal Global R&D, que va fabricar un xassís de moto complet amb la mateixa tècnica abans de construir els ancoratges testats al Dakar. Pedro Duro i Numa Guilhou, fundadors al seu dia de Duro Felguera i Fàbrica de Mieres i responsables que Astúries i l'acer portin units des de fa gairebé 200 anys, segur que somriuen des d'allà on siguin.
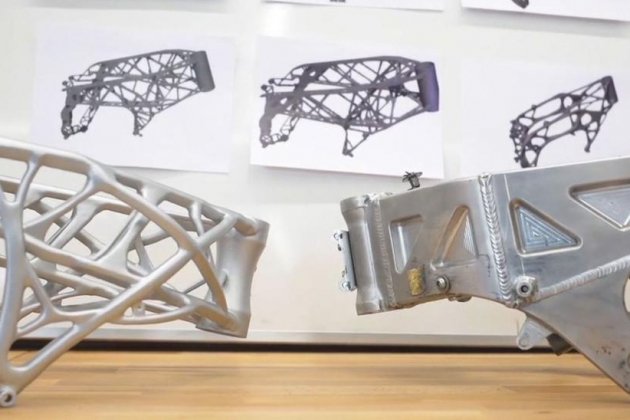