Asturias era carbón y acero y ahora, de los dos, sólo queda ya el acero, pero no un acero cualquiera: además de la única siderurgia integral de toda la península (la planta de Veriña), el Principado acoge en Avilés modernas acerías y un centro de innovación tecnológica en el que se desarrollan productos de todo tipo y se testan tecnologías disruptivas como la impresión 3D. Esta última técnica, precisamente, es la que se ha utilizado para fabricar componentes que ha utilizado uno de los vehículos que han competido en la última edición del Dakar.
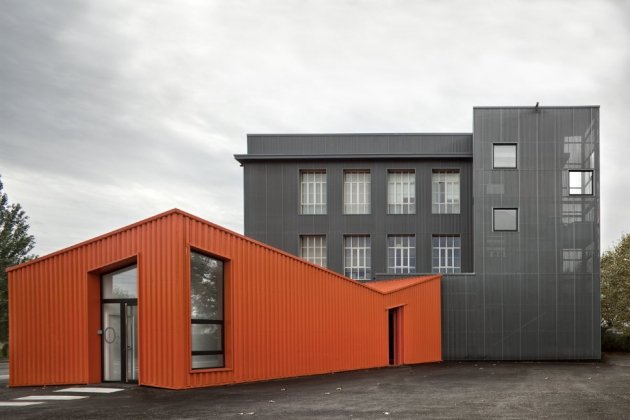
Los anclajes de un direccionador
Las piezas construidas en Arcelor Mittal Avilés forman parte del sistema de anclaje de los direccionadores laterales del Sodicars número 56 con el que los conquenses Manolo y Mónica Plaza (su hija) han competido este año en el rally. Plaza, propietario de una agencia de viajes de aventura, acumula con la de este año catorce participaciones en el Dakar. La pieza de acero fabricada en Avilés comn impresión 3D ha superado el test: sus 800 gramos (un 20% menos de lo que pesaría un componente fabricado en aluminio con métodos tradicionales) no ha planteado problema alguno.
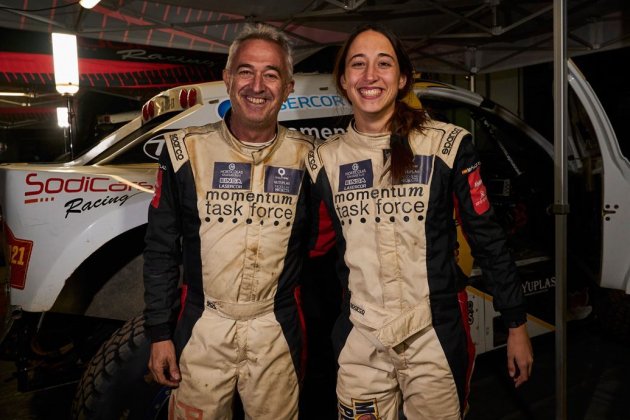
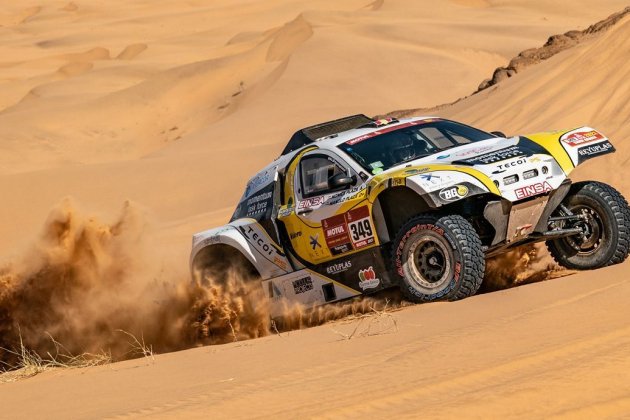
Nuevos caminos
El éxito, abre sin duda un nuevo nicho de negocio para Arcelor Mittal, que puede sin problemas ofrecer soluciones diseñadas digitalmente y construidas mediante fabricación aditiva a todos los sectores que se atrevan con este nuevo sistema. “En la movilidad futura, la fabricación aditiva seguirá teniendo un gran papel y el acero seguirá reinventándose para aprovechar nuevas oportunidades de desarrollo”, explican desde Arcelor Mittal Global R&D, que fabricó un chasis de moto completo con la misma técnica antes de construir los anclajes testados en el Dakar. Pedro Duro y Numa Guilhou, fundadores en su día de Duro Felguera y Fábrica de Mieres y responsables de que Asturias y el acero lleven unidos desde hace casi 200 años, seguro que sonríen desde allá donde estén.
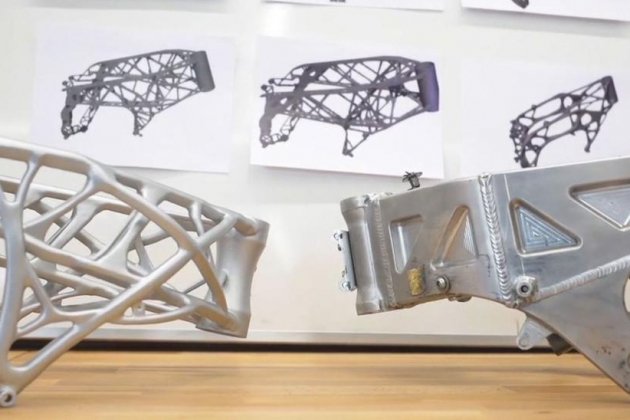